In this entry, I'm going to post the three first units of the first term. In this term, we studied Health and Safety at work.
UNIT 1: HEALTH AND SAFETY AT WORK.
First of all, we have to define the term "health". Health is a state of complete physical, mental and social well-being and not merely the absence of disease or infirmity.
Work can have positive and negative effects, and for that reason, we use 2 terms:
- Occupational risks: is the possibility that a worker suffers a certain damage arising from working conditions.
- Working condition: any work characteristic that may have an influence in the origin of risk related to the safety and health of the worker.In this are, we can highlight different aspects to take into account:
- Characteristics of premises, facilities, equipment, products…
- Physical, chemical and biological agents.
- Work organization.
- Procedures for using physical, chemical and biological agents.
After that, we need to explain the term Health and Safety at work.
Health and safety at work is a group of measures taking in order to prevent or reduce occupational risks and improve working conditions. It's regulated by the occupational health and safety legislation.
Occupational risk factors.
They can be organized in 4 groups:
Safety conditions.
|
Environmental conditions.
|
Ergonomic conditions.
|
Psychosocial conditions.
|
-Workplaces: premises, stairs, facilities…
-Work equipment: machinery, tools and transport equipment.
-Electrical and fire hazards.
|
-Physical agents: noise, radiation, lighting, temperature…
-Chemical agents: chemical.
-Biological agents: virus, bacteria, fungi, protozoa.
|
-Physical workload: physical effort, postures and manual freight-handling.
-Mental workload: amount of information, quick decision-making, attention level, responsibility.
|
-Work organization: variety of tasks, timetable…
-Personal traits: perfection in the task, motivation…
|
Worker's health damages.
Damage from work is defined as diseases, serious health conditions or injuries arising out of or in connection with work.
It's classified in 2 groups.
- Specified diseases: they’re a direct consequence from work.
- Work accident.
- Occupational disease.
- Non-specified diseases: they're a consequence from work, but also from other causes.
- Job dissatisfaction.
- Occupational tiredness, stress.
Work accident.
Work accident is any bodily injury suffered by the worker because of or as a consequence of working with others.
From the Occupational Health and Safety perspective, a work accident is an unexpected and unplanned event that interrupts the normal activity of the company and that can result in one or more workers incurring personal injuries.
There are some requirements needed to be considered as a work accident:
- Physical or psychic injuries.
- Working from others/hired hand workers: Self employed workers are also included if they contribute to Social Security for work accidents.
- Cause and effect relation between work and accident.
There are some cases that may cause misunderstanding, but they're included in legislation.
In itinere accidents.
|
Trade union office (cargo sindical)
|
Tasks not related or different.
|
Rescue actions (actos de salvamento)
|
Occupational diseases.
|
Accident consequences.
|
When going to work or going back home from work.
Without interruptions, usual itinerary and an adequate means of transport.
|
When doing union work (trabajo sindical)
|
When doing tasks not related/different to the worker’s professional group.
|
When performing rescue actions if they’re connected to work.
|
When contracting a disease at work not included in the list of occupational diseases and it’s proved in Court that in fact, it was contracted at work.
|
Accident consequences or complications that worsen the previous situations.
|
- General presumption: an accident is a work accident if it occurs during work timetable and at the workplace.
- Other cases considered as work accidents:
- In mission accidents→ during the timetable but not at the workplace.
- Professional neglicence→ excesive trust in the usual performance of the job.
There are some cases that aren't considered as work accidents. Among them:
- Force majeure accidents, such as an earthquake, a tsunami...
- Reckless endargement, for example, not wearing a harness.
There are 4 types of accidents, depending on the material and personal damages.
With personal injuries
|
Without personal injuries.
| |
With material damages.
|
Material damages+personal injuries (accidente típico)
|
Material damages but no personal injuries (accidente blanco)
|
Without material damages
|
Without material damages but with personal injuries (accidente caso)
|
Without material without personal injuries
(Incidente) (risk situation)
|
Accidents are caused due to a cause. It's divided in two categories; technical and human.
Technical causes.
|
Human causes.
|
-Facilities and workplace.
-Equipment, machinery, protection…
-Environment; lighting, noise…
-Work organization; shifts, night work…
|
-Lack of information and training.
*The worker doesn’t know that there’s a risk.
*The worker knows that there is a risk but doesn’t know how to act.
-The worker knows that there is a risk and knows how to act, but decides not to act.
|
Occupational disease.
Occupational disease list organized by activity sectors. It includes a list of possible diseases to be included in the future.
If the disease is due to work performance, but it’s not included in the list, it’ll have to be proven before Court.
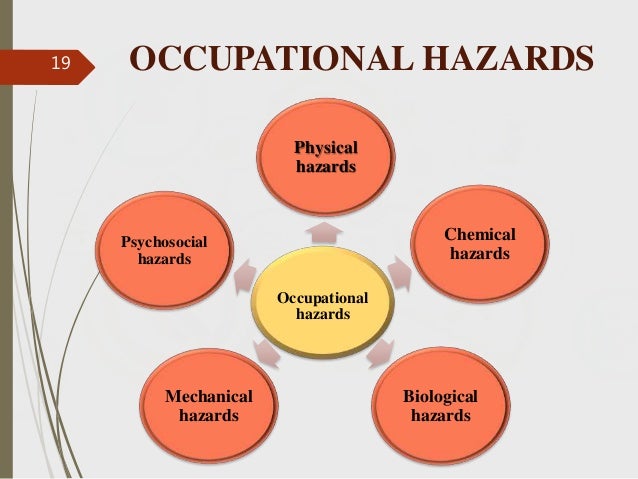
*Difference between work accident and occupational disease.
WORK ACCIDENT.
|
OCCUPATIONAL DISEASE.
|
Quick (puede pasar en cualquier momento)
|
Slow (se manifiesta a lo largo del tiempo)
|
Related to safety conditions.
|
Related to environmental conditions.
|
Identical effects.
|
Individual effects.
|
Prevention and protection measures.
*Prevention measures: they're carried out before something happens and the aim is to eliminate or reduce the cause.
Examples:
- Machinery and chemical substitution.
- Repairs and maintenance.
- Equipment initial design.
*Protection measures: they're carried out after something have happened and the aim is to eliminate or reduce the damage of the worker. There are two types of protection: collective and individual.
The collective protection involves the transmission medium (noise shields, banisters...) , and the individual one, is related to the worker (gloves, masks, helmets...)
*Health and safety disciplines.
Safety at work.
(Safety conditions)
|
Occupational or industrial hygiene.
(Environment)
|
Ergonomics.
(Ergonomical)
|
Psychosociology.
|
Occupational medicine.
|
Avoiding work accidents:
-Accidents information and statistics.
-Actions over facilities, machinery, equipments...
|
Preventing occupational diseases.
-Environmental pollutants measuring.
|
Avoiding fatigue through job-person adaptation.
|
Working against labour dissatisfaction through labour organization.
|
Preventing health loss:
-Check-ups.
-Recovery.
-Rehabilitación.
|
*Collective protection measures.
They protect several workers. They don't avoid risks, but try to reduce or avoid the damage.
Examples:
- Banisters or railings and safety nets.
- Machinery safety guards (to avoid blows, cuts or trapping.)
- hotoelectric cells or double control).
- General air circulation/ ventilation (to lower/avoid the presence of chemicals)
- Shields (to avoid particles projection); noise shields)
*PPE; personal protective equipment.
They're the last prevention measure. They're the equipment designed to protect the wearer's body and minimize exposure to serious workplace injuries or illnesses.
Examples:
- Head→ helmets.
- Inner ear→ earmuffs, earplugs.
- Eyes and face→ goggles,shields.
- Hands and arms→ gloves.
- Legs and feet→ safety footwear.
- Trunk and abdomen→ vests.
- Respiratory tract→ masks.
- Body in general→ harness, safety clothing.
UNIT 2. HEALTH AND SAFETY AT WORK: LEGISLATION AND ORGANIZATION.
Occupational Health and Safety legislation: Law framework.
There are four levels on the law framework:
- International standards.
- ILO.
- EU legislation.
- Spanish Constitution.
- Art. 40.2.
- Bacic legislation.
- Occupational Risk Prevention Act 31/1995.
- Regulations for Prevention Services RD 39/1997.
- Specific legislation.
- Royal decrees.
Duties in Occupational Health and Safety.
Workers have duties in Health and Safety at work, among them:
- Implementing and applying an occupational risk prevention plan.
- Assesing occupational risk when they can't be avoided.
- Providing work equipment and protection measures.
- Provide personal protective equipment (PPE- EPI’s).
- Preparing an emergency plan.
- Adopting measures in case of serious and imminent danger.
- Informing and training.
- Consultation and participation.
- Health surveillance.
- Maternity and breastfeeding protection.
- Protection of special risk groups.
Workers also have duties:
- Use properly the PPE's, machines, tools and not putting out of operation safety devices.
- Informing immediately superiors or safety representatives of risky situations.
- Cooperating with the employer in Occupational Health and Safety issues.
Liabilities in Occupational Health and Safety issues.
*Employer:
- Offences in occupational health and safety issues involve a penalty.
- Types of responsibility:
- Administrative liability: minor, major and serious offence.
- Public liability: economic compensation to the worker for personal damages.
- Criminal liability: seriously jeopardize worker’s lives, health or physical integrity.
- Surcharge on Social Security benefits: when the accident has been a direct consequence from the lack of prevention measures.
*Worker:
If they don't carry out that liablities, they can be punished by the employer.
If they don't carry out that liablities, they can be punished by the employer.
- Minor, major and serious misconducts→ collective bargaining agreement.
- Offence→ from verbal warning to disciplinary dismissal.
*Labour Inspection role:
Labor Inspection is an institution that supervises the compliance of labour and occupational health and safety law.
Its tasks are:
- Visiting the companies whenever they want.
- Issuing offence reports and propose penalties.
- Giving warning and requirements.
- Ordering immediate stoppage.
- Preparing accidents reports.
Occupational Health and Safety organization.
Employers must plan and organize Health and Safety at work.
Types:
- Personally assuming prevention activities:
- Companies with less than 25 employees and just one workplace.
- For health surveillance, they must follow a different organization type.
- If there's special risk activities→ employers can’t assume prevention activities.
- Appointing one or several workers to carry prevention activities out.
- The employers names one or several workers to manage health and safety at work.
- Enough training resources and time to manage prevention activities.
- Guarantees not to be dismissed.
- Establishing an internal prevention service.
- Companies with more than 500 workers→ compulsory.
- Companies between 250-500 workers + special risk activities→ compulsory.
- Because of danger and or occurred accidents, if labour authority decides so.
- Joint prevention services → several companies sharing the same physical space establish a joint prevention service.
- Contracting an external prevention service.
- Organizations specialized in managing health and safety at work.
- One of the most used options.
Worker's participation in Occupational Health and Safety.
- Safety representatives.
- Designated by and among workers' representatives.
- Health and Safety Committee.
- Companies with at least 50 workers and works council.
- Set up by safety representatives and company’s representatives in the same proportion.
- When there are more than 50 workers→ health and safety committee.
- All members must have a basic level training in health and safety at work.
- Competences and powers.
- Do the prevention plan.
- Assess risks.
- Establish performance priorities.
- Health surveillance.
- Training and information to workers.
- First aid and emergency plans performance.
Occupational Health and Safety management.
There are some principles of preventive action. The following:
- Avoiding risks.
- Assessing risks that can’t be avoided.
- Fighting risks at source.
- Replacing dangerous equipment, tools, chemicals...by non-dangerous or less dangerous ones.
- Planning prevention and protection activities.
- Giving priority to collective protection measures over the personal ones.
- Giving appropriate instructions to workers.
- Job-person adaptation.
- Taking into account technical progress.
Occupational risks assessment.
Initial and regular assessment have to be carried out.
For assessing if there are occupational risks, we use the INSHT risk assessment method.
Consequences of severity.
| ||||
Probability.
|
Slightly harmful (cuts, headaches…).
|
Harmful (burns, deafness, asthma).
|
Extremely harmful (amputations, intoxications, fatal accidents).
| |
Low (rarely, hardly ever).
|
Trivial.
|
Tolerable.
|
Moderate.
| |
Medium (occasionally).
|
Tolerable.
|
Moderate.
|
Important.
| |
High (always, nearly always).
|
Moderate.
|
Important.
|
Intolerable.
|
- Trivial→ specific actions aren’t required.
- Tolerable→ prevention measures don’t need to be improved. However, more cost-effective solutions or improvement should be considered. Regular checks.
- Moderate→ efforts to reduce the risk should be made.Measures to reduce the risk should be implemented within a fixed period of time.
- Important→ work shouldn’t start until the risk has been reduced. If the work is being carried out, the risk must be reduced in less time than in a moderate situation. Considerable resources may be needed.
- Intolerable→ work shouldn’t start or continue until the risk has been reduced. Stop immediately.
Working accidents management.
*Accidents investigation, accidents to investigate:
- Fatal and serious accidents (mortales y graves) → ALWAYS.
- Minor accidents, incidents and accidentes blancos that occur repeatedly, involve a potential risk of serious injuries or with unknowns causes.
*Accidents record (own business) and notification (labour authority):
- Employers must record and notify them via Internet.
- It’s compulsory to notify those that imply at least 1-day medical leave. Companies must also notify a monthly list of accidents without medical leave.
- Internally→ it’s voluntary to register those accidents without medical leave.
Accidents costs.
Accidents lead not only in cost for companies, but also for the worker and society.
*Costs for companies:
- Salaries and compensations to workers.
- Productivity loss after the accident.
- Downtime (tiempos perdidos) in helping the victim.
- Downtime in investigating and notifying the accident.
- More labour disputes.
- Material damages.
- Economic and criminal penalties.
- Image loss.
*Costs for the worker and the family:
- Pain and suffering.
- Professional capacity loss.
- Temporary or permanent income decrease.
*Costs for the society:
- Human resources loss because of death.
- Productive capacity loss due to permanent disabilities.
- Social Security compensations.
- Accident management by Labour Inspection.
- Labour trials…
UNIT 3. HEALTH AND SAFETY AT WORK: OCCUPATIONAL RISK FACTORS AND THEIR PREVENTION.
Occupational risk factors.
Safety conditions.
|
-Workplaces.
-Work equipment.
-Electrical and fire hazard.
|
Working accidents.
|
Environmental conditions.
|
-Physical agents.
-Chemical agents.
-Biological agents.
|
Occupational diseases.
|
Ergonomic conditions.
|
-Physical workload.
-Mental workload.
|
-Physical fatigue.
-Mental fatigue.
|
Psychosocial conditions.
|
-Work organization.
-Personal traits.
|
-Job dissatisfaction.
-Stress.
-Mobbing.
-Burnout.
|
Safety conditions: Occupational risk factors.
Workplaces.
Royal Decree 486/1997→ Establishes the minimum conditions about Health and Safety at the workplaces.
Structures and floors.
|
Solid and able to support weight.
Stable, non-slippery, without excessive slopes
|
Workspaces.
|
Minimum 3 m of height, 2 m2 per worker and 10 m3 of volume per worker.
|
Banisters or railings.
|
Minimum 90 cm of height with toeboard.
|
Stairs and pathways.
|
Stairs→ width 1 m.
Doors→ min. width 80 cm; corridors 1 m.
|
Evacuation exits.
|
Clear, marked, with safety illumination and doors that open outwards.
|
*Damages,prevention/protection measures.
Damages.
|
Prevention/Protection.
|
Slips.
|
Following legislation about safety and health at workplaces.
|
Falls of people and objects.
|
Safety signs.
|
Blow with objects.
|
Organization and cleanliness.
|
Protection with safety nets and fall protection harness.
|
Machines and tools.
*Machinery is one of the main occupational risks in working accidents. it usually causes serious personal injuries.
*Damages, prevention/protection measures.
Damages.
|
Prevention/Protection.
|
Blows, cuts, amputations, burns, electrical and fire hazards, deafness…
|
In the machine design so that it doesn’t become a risk in itself.
|
CE marking→ it guarantees that the machine follows safety legislation.
| |
Collective protection measures.
| |
Suitable PPE’s.
| |
Avoiding the use of loose-fitting clothes, necklaces, bracelets, rings…
|
*Tools→ they cause frequent working accidents, but with minor consequences.
*Damages, prevention/protection measures.
Damages.
|
Prevention/protection.
|
Blows, particles projection and electrical contacts.
|
Using tools just for the purpose for which they are intended.
|
Tools use training.
| |
Maintenance.
| |
Appropriate transport.
| |
Organization and cleanliness.
|
Electrical hazards.
It’s the possibility that electricity passes through human body. There are two ways of receiving an electric shock.
There are 3 types of contacts:
Direct contact.
|
-Directly touching a live conductor or live part.
|
Indirect contact.
|
Touching metalwork which has been made life by a fault in the electrical installation.
|
High-voltage contacts.
|
Approaching devices with more than 1.000 volts
|
*Damages, prevention/protection measures.
Damages.
|
Prevention/protection.
|
Measures concerning workers.
| ||
Depend on several elements: electric current intensity, he time the contact lasts and the electric current path.
It can go from tickless to cardiorespiratory arrest, serious burn or death.
|
Direct contact.
|
Indirect contact.
|
High voltage contact.
|
Safety signs information.
|
Moving away life parts.
|
Earth wires.
|
Safety signs information.
|
PPE.
| |
Barriers.
|
Residual current circuit breakers.
|
Insulation tools.
|
Insulation tools.
| |
Insulation of cables or parts required in installations.
|
Other measures of passive protection: electrical separation.
|
Checking the lack of power and indicating the development of electrical works before starting.
|
Fire hazards.
*Fire→ Uncontrolled fire that destroys something that wasn’t meant to burn.
*Fire tetrahedron→ Necessary elements to start a fire and maintain it in time.
- Fuel: any substance that can undergo combustion.
- Oxidizing agent: air containing oxygen.
- Heat: heat energy enough to release vapour from fuel and cause ignition.
- Chain reaction: part of the initial heat dissipates, while the other part is reused as activation energy.
*Classes of fires→ according to the type of fuel.
- Class A: solids.
- Class B: liquids.
- Class C: gasses.
- Class D: metals.
*Damages, prevention/protection measures.
Damages.
|
Prevention/protection.
|
Death.
|
Workers training.
|
Internal and external burn.
|
Fire extinguishers.
|
Entanglements and avalanches due to the panic.
|
Building designs.
|
Smoke-detecting and temperature-detecting devices.
| |
Appropriate storage of inflammable substances and products.
|
Environmental conditions: occupational risk factors.
Physical agents.
1. Noise.
Noise is defined as an unwanted or damaging sound. It's measured in decibels.
The maximum exposure levels are 87 dB for continous/ intermittent noise and a peak level of 140 dB for impact noise.
*Types of noise:
- Continuous noise: doesn’t change, it’s constant.
- Intermittent noise: it occurs intermittently.
- Impulsive or impact noise: noise consisting of single burst with a duration of less than 1 second.
*Damages, prevention/protection measures.
Damages.
|
Prevention/protection.
|
Measures on workers.
|
Headaches, irritability, digestive problems, deafness, auditory fatigue, stress, insomnia…
|
Replacement of machinery and noisy facilities.
|
Information and training and PPEs.
|
Maintenance of noisy facilities.
| ||
Reducing workers’ exposure time.
| ||
Medical checkups >80 dB (every 5 y) and >85 dB (every 3y)
| ||
Safety signs in noisy areas.
| ||
Offer specific PPE’s (+80 dB) +85 dB it’s compulsory.
|
2. Vibrations.
Vibration is defined as a rapid movement to and fro or oscillating movement.
*Types:
- Hand-arm vibration: jackhammer.
- Whole body vibration: driving a bus.
*Damages, prevention/protection measures.
Damages.
|
Prevention/protection.
| |
Hand-arm vibration.
|
Whole body-vibration.
|
Machinery and tools design.
|
Vibration white finger or Raynaud's syndrome.
|
Backaches, lower back pain, hernias…
|
Taking breaks.
|
Elbow osteoarthritis.
|
Dizziness, vomits.
|
PPEs.
|
Wrist injuries.
|
Information and training.
| |
Using anti-vibration seats in vehicles.
|
3. Radiation.
Radiation is defined as the energy that travels through space and we live with, such as x-rays, ultraviolete rays...
*Types:
- Ionizing radiation: radiation that carries enough energy to cause: cell death, cancer and modifying genetic code.
- Non-ionizing radiation: the least dangerous.
Damages.
|
Prevention/protection.
| |
Ionizing radiation.
|
Non-ionizing radiation.
|
Safety signs in risk areas and compulsory use of PPE.
|
Occupational cancer.
|
Burns and skin injuries.
|
Regular medical check-ups.
|
Effects on reproduction.
|
Conjunctivitis, cataracts.
|
Reducing exposure time.
|
Compulsory PPE.
| ||
Information and training.
|
4. Temperature.
Human body needs to maintain a constant temperature of 37ºC.
*Damages, prevention/protection measures.
Damages.
|
Prevention/protection.
| ||
Excessive heat.
|
Excessive cold.
|
Excessive heat.
|
Excessive cold.
|
Heat stroke: fever, tachycardia, headache, unconsciousness and death.
|
Hypothermia: muscle and heart problems, hallucinations and death.
|
Natural or artificial air circulation.
|
Acclimatazing premises with heaters or heating.
|
Fainting: heat exhaustion, dizziness, cramps.
|
Partial cooling.
|
Following legislation about minimum temperatures.
|
Insulating premises avoiding air currents.
|
Reducing exposure time.
|
Reducing exposure time.
| ||
Wearing suitable clothes and drinking water frecuently.
|
Wearing suitable clothes.
|
5.Lighting.
The measure unit is called "Lux".
*Damages, prevention/protection measures.
Damages.
|
Prevention/protection.
|
Many accidents are caused by insufficient light.
|
Using natural light whenever it’s possible.
|
Eye fatigue and tiredness.
|
Having general and localized illumination.
|
Avoiding contrasts and dazzles.
| |
Following the legislation about the minimum quantity of lux at workplaces.
|
Chemical agents.
There are 3 types of chemical agents:
- Solid:powders in suspension in the air, fibers, smoke.
- Liquid:aerosols, fog.
- Gases: carbon monoxide.
*Damages:
Irritant→ make the skins red or blister.
Corrosive→ destroy tissues.
Suffocating→ prevent breathing.
Anaesthetic→ sleepiness and loss of consciousness.
Sensitizing→ allergic reactions.
Carcinogenic and mutagenic→ cancer and genetic alterations.
Pneumoconiotic→ they accumulate in lungs causing muscular problems and death.
Systemic→ affect different organs at the same time.
*Prevention/protection measures.
- Occupation or industrial hygiene.
- Replacing or reducing pollutants.
- Regular measurements.
- Keeping at a distance the pollutant.
- Reduce the exposure time.
- Information and training.
- Suitable PPEs.
Biological agents.
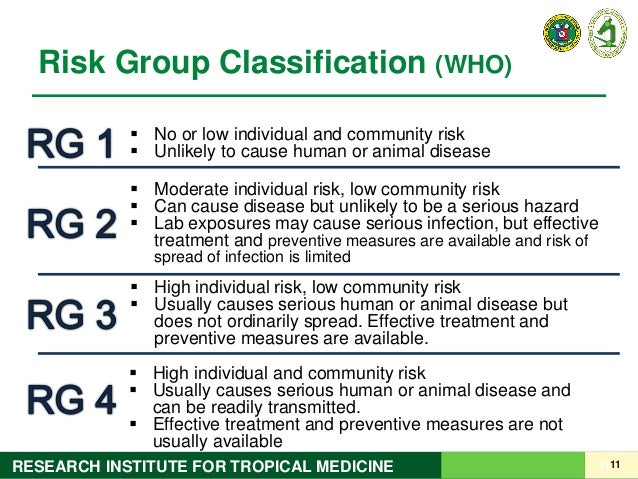
Biological agents, are microorganisms that penetrate the human body causing contagious and parasitic diseases: virus, protozoa, fungi, bacteria…
The contagion is through contact with other people, animals or contaminated material.
*Ways of entering the human body.
- Respiratory system.
- Digestive system.
- Skin or injuries.
The workers that are in risk are: health care and laboratory workers, agriculture and cattle workers or vets.
*Risk group classification:
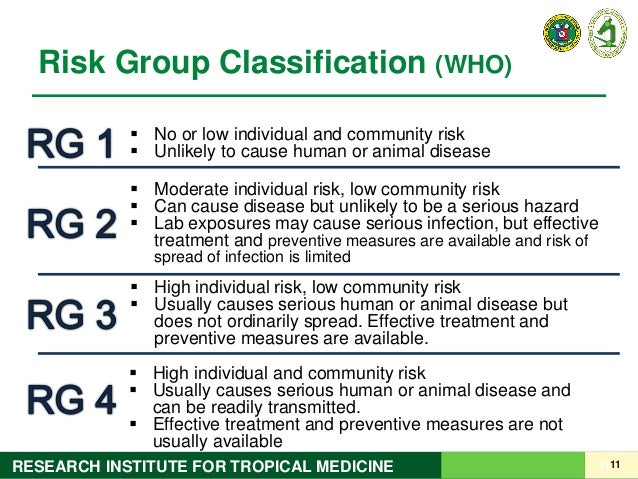
*Damages, prevention/protection measures.
Damages.
|
Prevention/protection.
|
Hepatitis B.
|
Preventive medicine: vaccines and regular check-ups.
|
AIDS.
|
Suitable hygienic conditions at workplaces.
|
Tuberculosis.
|
Disinfection and sterilization of healthcare tools.
|
Tetanus.
|
Having 10 minutes for changing clothes and for personal cleanliness.
|
Brucellosis or Malta fever.
|
Not mixing up working clothes with personal ones.
|
Not eating or drinking at the workplace.
| |
PPE’s.
| |
Information and training.
|
Ergonomic conditions: occupational risk factors.
1. Physical workload.
- Workload: physical and mental demands required in a job.
- Physical demands: physical workload.
- Mental demands: mental workload.
- Physical workload: tasks with muscular effort. It includes 3 factors:
- Physical efforts and repetitive movements.
- Incorrect or poor postures.
- Manual load handling.
*Damages, prevention/protection measures.
Damages.
|
Prevention/protection.
|
Tendinitis.
|
Correct postures.
|
Lower back pain.
|
Training.
|
Hernias.
|
Replacing manual load handling with mechanical equipment.
|
Neck pain.
|
Suitable and trained staff in manual handling and physical efforts.
|
Carpal tunnel syndrome.
|
Reducing exposure time.
|
Tennis elbow.
|
Stretching and relaxing exercises.
|
Physical fatigue.
|
2. Mental workload.
- Mental workload: mental demands that can cause mental fatigue due to:
- The quantity of information used.
- Complexity and time available to fulfil the task.
*Damages, prevention/protection measures.
Damages.
|
Prevention/protection.
|
Tiredness and exhaustion.
|
Taking breaks.
|
Headaches.
|
Adapting the quantity of information.
|
Stress.
|
Avoiding noise at the workplace.
|
Irritability.
|
Following regulations about display screen equipment.
|
Insomnia.
|
3. Display screen equipment.

*Damages, prevention/protection measures.
Damages.
|
Prevention/protection.
|
Visual fatigue.
|
Taking breaks.
|
Muscular fatigue.
|
Avoiding constrasts and dazzles.
|
Headaches, insomnia, irritability, stress...
|
Medical check-ups.
|
Avoiding noise at the workplace.
| |
Information and training.
|
Psychosocial conditions: occupational risk factors.
In psychosocial conditions interact:
- Company's characteristics.
- Worker's characteristics.
Psychosocial conditions.
| |
Working time.
Long working hours, without breaks, shifts, night work...
|
Work organization.
Instability, low salaries, excessive supervision...
|
Job characteristics.
Monotonous, autonomy, rhythm, expectations...
|
Worker’s characteristics.
Academic education, complementary or additional training, worker’s ability, personality and emotional intelligence.
|
*Damages, prevention/protection measures.
Damages.
|
Prevention/protection.
| |||
Job dissatisfaction.
|
Working times.
|
Work organization.
|
Job characteristics.
|
Work characteristics.
|
Occupational burnout.
|
Avoiding long working hours.
|
Job rotation.
|
Avoiding ambiguity in the contract of employment.
|
Information and training.
|
Work stress.
|
Taking breaks.
|
Allowing autonomy in the decision making progress.
|
Fair salaries.
| |
Harassment at work.
|
Knowing shifts in advance.
|
Staff recruitment according to the position.
|
Participative leadership style.
| |
Positive work environment.
|
- Job dissatisfaction: negative attitude towards work due to the difference between expectation and reality.
- Occupational burnout: job dissatisfaction extended in time.
- Being emotionally exhausted.
- Loss of enthusiasm.
- Negative attitude towards job, customers, and colleagues.
- Work stress: imbalance between work demands and resources to accomplish work.
- Harassment at work: continuous and deliberate mistreatment with the purpose of making the worker unstable and psychologically weakening him.
- Digestive disorders, sleep disorders, anxiety, depression…
Self protection plan.
It’s compulsory that companies prepare an emergency plan that it’s included in the self-protection plan.
*Emergency plan:
The emergency plan is a document with procedures for handling unexpected situation.
It includes:
- Possible emergency situations and measures needed.
- Designated personnel.
- Coordination with external services.
*Self-protection plans.
The self-protection plan is a document with the aim of preventing and controlling risks. It's prepared by a technician.
In the document, procedures for handling emergency situations are specified.
There's a coordination with Protección Civil.
No hay comentarios:
Publicar un comentario